Rolls Royce: testare un motore a jet in condizioni estreme
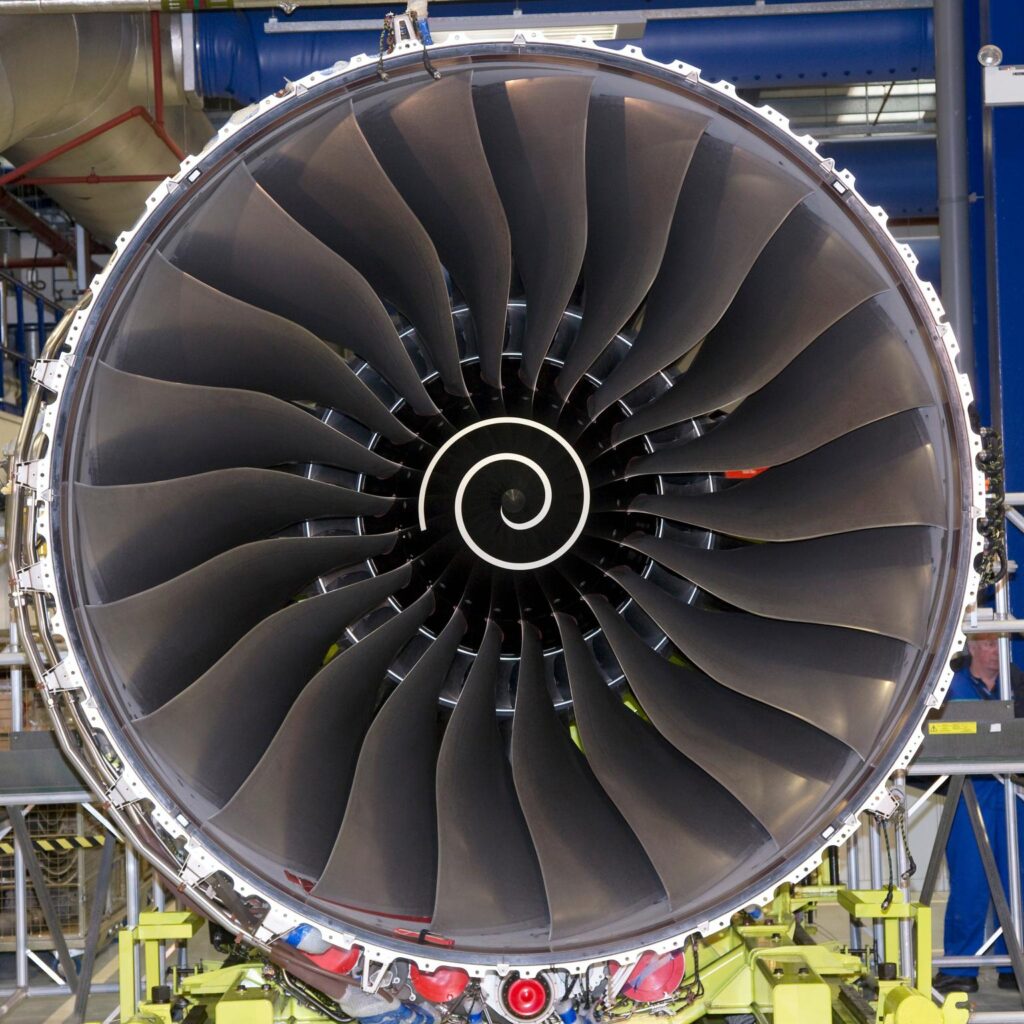
Ad oggi gli aerei civili coprono quasi tutti i luoghi abitati volando in condizioni meteo molto disparate: sorvolano terra, mare, sabbia, neve, attraversando tempeste estreme. In ognuno di questi casi, il motore deve garantire il corretto funzionamento con efficienza e prestazioni previste, in sicurezza e, non ultimo, in relativo silenzio.
Ecco come Rolls Royce testa un motore a jet, spingendolo al limite delle capacità operative per garantirne il funzionamento in condizioni estreme.
Ambiente operativo di un motore a jet
Mentre temperatura e pressione in cabina sono costantemente regolate, le condizioni esterne variano notevolmente lungo tutto il profilo di missione del velivolo.
Ad esempio, la temperatura alla quota di crociera (40000 piedi o 10 km) è solitamente intorno ai -60 °C. In queste condizioni si ha una rapida formazione di ghiaccio sulla parte frontale della presa d’aria che deve rompersi prima di danneggiare il motore.
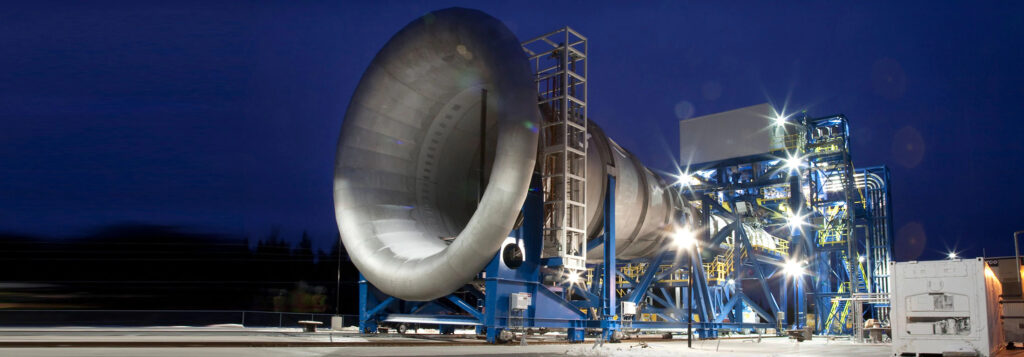
Credits: Rolls Royce
Rolls Royce testa queste condizioni su un motore a jet presso la struttura GLACIER (Global Aerospace Centre for Icing and Enviromental Research) in Manitoba, Canada. In questa zona sub-artica le temperature raggiungono i -40°C durante la stagione invernale. Qui una serie di test valuta il limite fisico dei grandi motori a ciclo turbogas in queste condizioni estreme di temperatura.
Inoltre si provvede anche a testare l’accensione con temperature ghiacciate, volendo simulare il tentativo di riaccensione del motore in crociera: a queste temperature l’olio motore diventa un elemento critico perché assume una densità altissima.

Credits: Rolls Royce
La necessità di decollare, volare ed atterrare attraversando forti piogge e tempeste richiede che il motore sia adeguatamente resiliente ai cambiamenti atmosferici.
Tuttavia, in presenza di grandine e forti raffiche di vento, vi è il serio rischio che palle di ghiaccio entrino all’interno della presa d’aria. Per prevenire ciò, Rolls Royce testa il motore a jet annegandolo con acqua per valutare la tenuta della fiamma in queste condizioni.
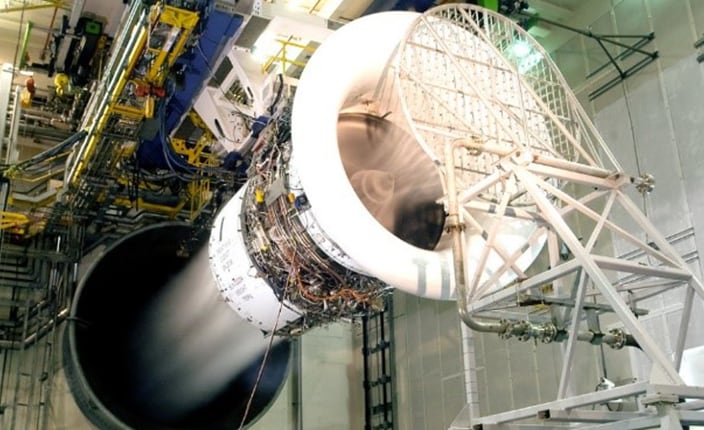
Credits: Rolls Royce
Volo no-stop
Un motore aeronautico è progettato per essere sempre in funzione, fermandosi sol durante i rapidi rifornimenti e scali. Si pensi che il volo più lungo attualmente operativo è Newark – Singapore, della durata di circa 18 ore.
Gli aerei che percorrono questa tratta sono propulsi dallo stato dell’arte di Rolls Royce, il Trent XWB: un motore della 6° generazione di Trent, progettato con l’esperienza accumulata da oltre 70 milioni di ore di volo. Esso promette, insieme al gioiello di General Electric, di rivoluzionare gli standard di consumo e prestazioni dei velivoli a lungo raggio.
Un test di durata permette la certificazione del motore a stress prolungati, per verificare che questo ed i suoi componenti lavorino in sicurezza. Rolls Royce ha recentemente concluso una simulazione sul Trent XWB lunga l’equivalente di oltre 1000 voli a lungo raggio no-stop, presso un’apposita struttura in Thailandia.
Fase finale di certificazione di un motore a jet
I requisiti sulla certificazione dei motori aeronautici includono anche il controllo del rumore. Infatti, tutta l’industria aeronautica sta lavorando per rispettare il target del 2050: il rumore prodotto dai motori a jet scenderà del 65% rispetto a quello attuale e l’impatto ambientale sarà nullo.
L’inquinamento acustico viene valutato, con precisione di frazioni di decibel, presso il NASA Stennis Space Center. Microfoni incredibilmente sensibili vengono disposti intorno al sito di test per misurare il rumore ad ogni livello di spinta. La presa d’aria è coperta da quella che sembra una enorme palla da golf per evitare che la turbolenza di terra influenzi il rumore prodotto.
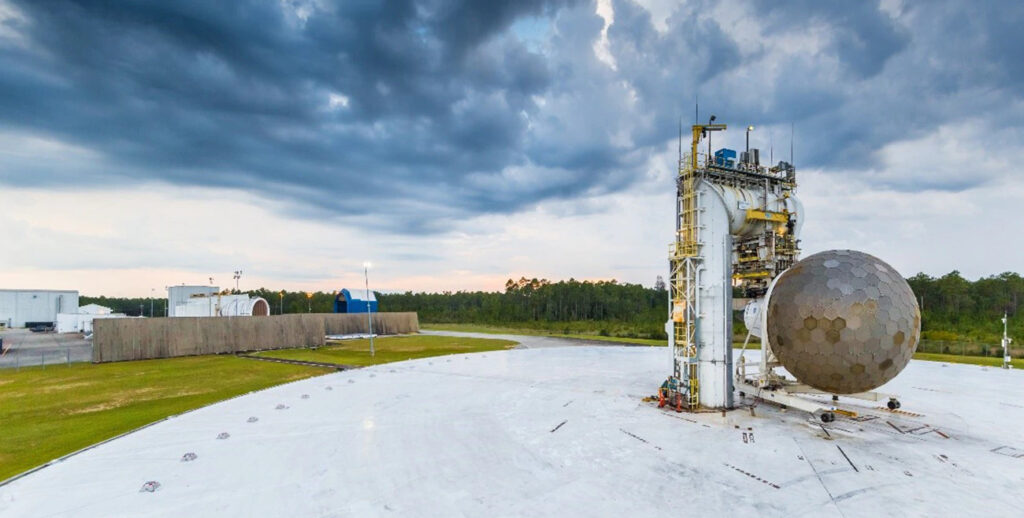
Credits: Rolls Royce
I motori aeronautici sono dei veri e propri gioielli di ingegneria, delle macchine capaci di erogare quantità enormi di potenza in qualsiasi condizione atmosferica. I moderni motori sono inoltre in grado di garantire l’operatività di un velivolo anche nel caso in cui uno dei due smettesse di funzionare.
I requisiti di sicurezza sono molto stringenti: la gondola (ovvero il guscio) deve essere in grado di contenere l’eventuale esplosione del motore, dovuto ad esempio alla rottura di una paletta in seguito all’impatto con un uccello.
Per verificare che questa sicurezza sia garantita, ogni motore viene distrutto in maniera controllata, facendo esplodere una pala del fan mentre esso sta girando alla massima potenza.
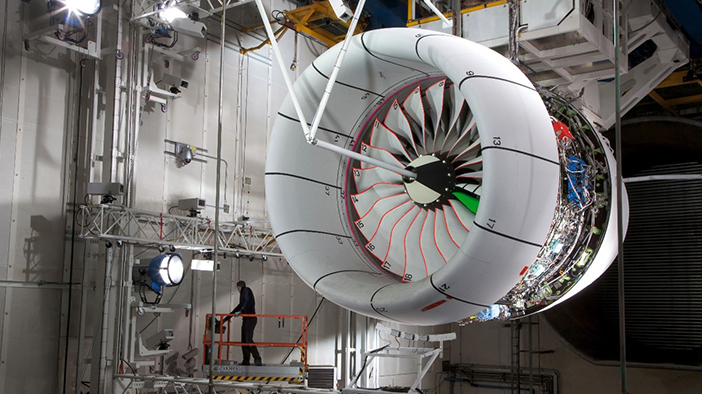
Credits: Rolls Royce
Una volta condotto anche il test a rottura, il propulsore viene montato su un Boeing 747-200 e testato in volo sopra i cieli dell’Arizona. Attualmente Rolls Royce sta convertendo un Boeing 747-400, ritirato da Qantas dopo 20 anni di servizio, per ampliare la flotta di piattaforme test.
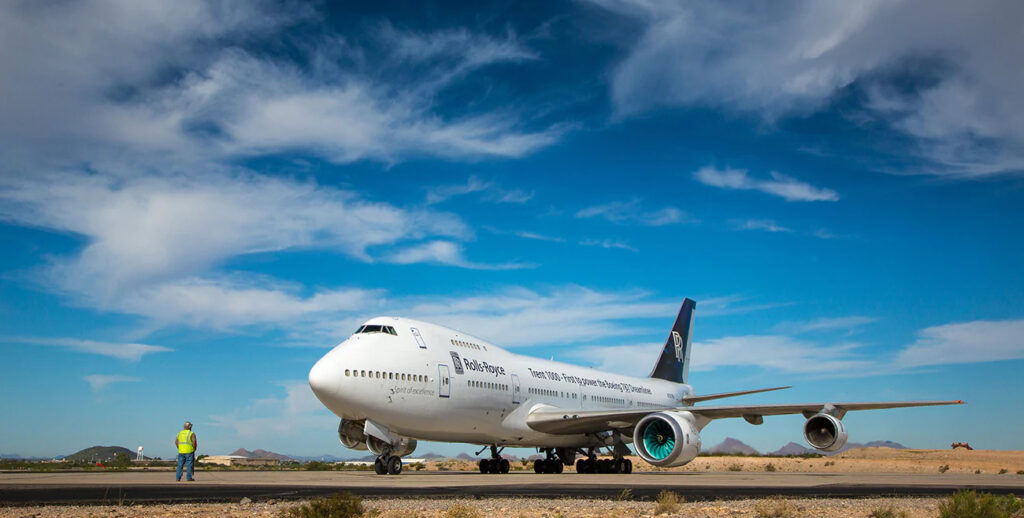
Credits: Rolls Royce
Guardando verso il futuro
Rolls Royce e General Electric continuano a spingere e testare nuove configurazioni con l’obiettivo di progettare il più efficiente e pulito sistema di produzione potenza al mondo, sempre più connesso digitalmente con l’intero velivolo.
I moderni aeroplani sono infatti equipaggiati con sistemi digitali di controllo motore, come il FADEC, necessari a controllare più variabili contemporaneamente. Gli stessi sistemi di controllo termico del motore sono totalmente interdipendenti con la linea digitale.
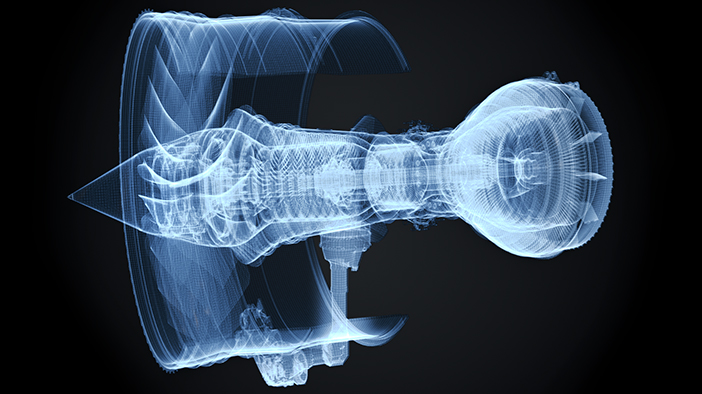
Credits: Rolls Royce
Attualmente Rolls Royce sta costruendo la più grande e funzionale piattaforma di test al mondo presso Derby, Inghilterra. Oltre ad essere una struttura enorme, essa sarà in grado di testare il motore a getto fisicamente e digitalmente con le più avanzate tecnologie.
Il Testbed 80 rappresenta il futuro punto di forza di Rolls Royce per testare i propri motori a jet. Sarà un sito fondamentale per lo sviluppo dei nuovi concept ibridi ed elettrici e dei futuri turbofan in configurazione UltraFan. Quest’ultimo concept prevede di diminuire del 25% il consumo e la produzione di anidride carbonica.
La piattaforma permetterà anche di testare nuove soluzioni di jet fuels per un futuro più green: i SAF (Sustainable Aviation Fuel).
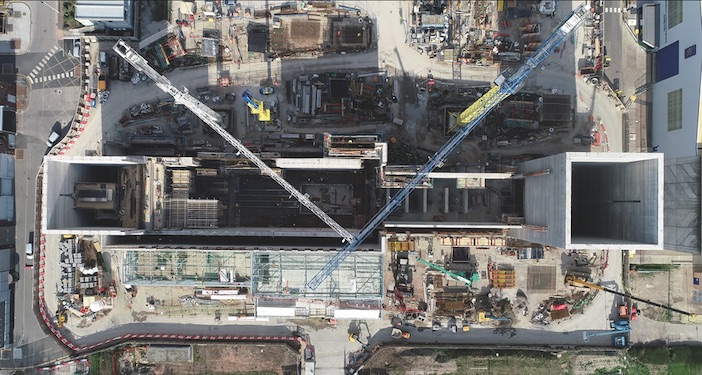
Credits: Rolls Royce
Testbed 80 è il simbolo di come l’intelligenza artificiale consenta di monitorare oltre 10 000 differenti parametri di un motore attraverso un complesso sistema di sensori che registra oltre 200 000 campioni al secondo.