3D Spacer Fabrics: preforms for fabrics reinforced composites
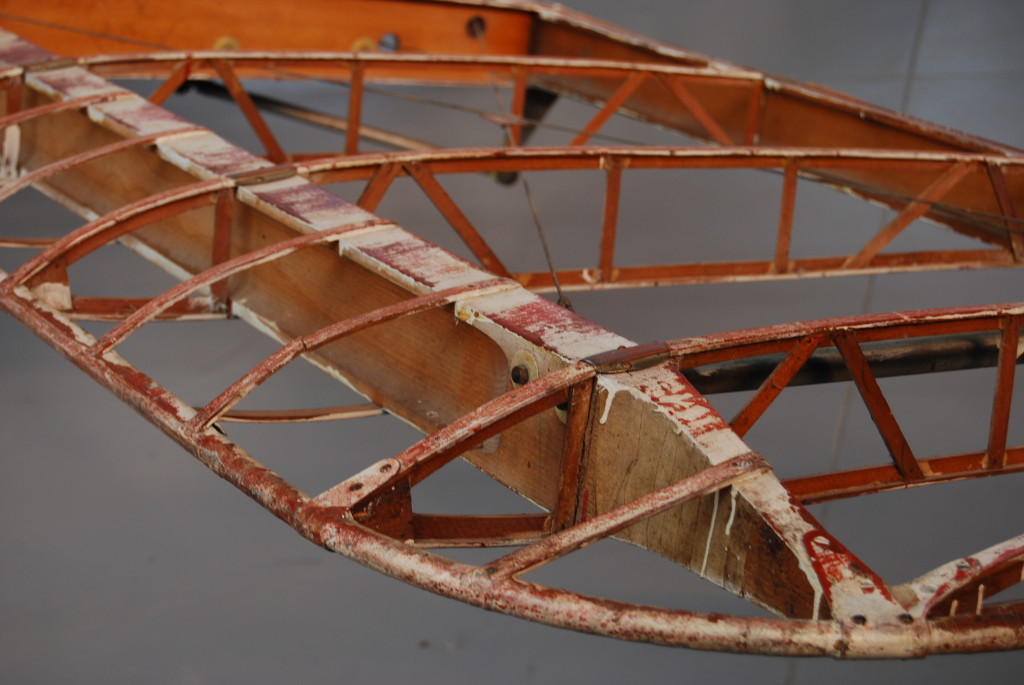
wikipedia.org
The use of fabrics in the aircraft industry dates back to the construction of the wings of kites and gliders adopted in early studies on the flight, and the creation of the first hot air balloons and hydrogen balloons. The first flight with a motorized vehicle supported with a human on board is attributed to the Wright brothers, who flew up in 1903 with a glider with wooden structure, very light, covered with canvas satin cotton. Subsequently, the initials wooden structures have left the place gradually to metal structures, which provide greater mechanical performance and longer life. Since World War II, Americans have always associated the idea of metal aircraft with the concept of resistance, but the development of composite materials in the second half of the ‘900 has revolutionized the way of thinking and designing aerospace structures, so that today they flank the predominant use of steel alloys and aluminum.
Over the past 150 years, human activity has caused climate change such that it is believed the global surface temperature will rise by 1.1° C to 6.4° C during the twenty-first century. The G8 countries have decided to limit global warming to 2° C and reduce their greenhouse gas emissions about 80 % by 2050.
As the world’s CO2 emissions caused by the combustion of fuel for transport are currently 24 % of the total emissions of man-made and are still expected to increase, it is necessary to reduce such emissions: an important step for this purpose was the development of composite materials. In particular, fabrics reinforced composite can reduce the weight of vehicles and their manufacture is considered cheaper, faster and easier than cast aluminum and steel. They generally consist of a polymeric matrix and as the second stage: high performance fibers, which are fibers of glass, carbon or aramid and for their production can be achieved preforms using the innovative Spacer Fabrics 3D.
The Spacer Fabrics 3D buildings are constituted by two external flat layers connected by a connecting layer, typically made from yarns said spacer, that make the three-dimensional structure. The interior link layer is characterized by alternating yarn and gaps and it ensures that the structure is not crushed under the influence of an external pressure. In fact, the distance between the two surfaces remains constant during compression thanks to the resilience of the yarn that separates them.
The traditional Spacer Fabrics can be replaced by Spacer Fabrics in which layers of fabric are used as a link instead of yarn, to obtain greater strength along the z-direction. They are significantly advantageous for the realization of textiles preforms in lightweight composite, thanks to properties such as the 3D arrangement of the fibers, the possibility of using different materials, the reduction of mass per volume, which depend on variables such as the material of the yarn, the distance between the surface layers and the technology used for the construction of the fabric.
The application of preforms reinforced with fabrics requires the development of intricate geometry. It is, in fact, necessary diversification of geometric Spacer Fabrics in order to develop preform compatible for components of complex shape. Thanks to modern knitting machines can perform various multilayer structures or curvilinear and tubular structures. The realization of preforms for high-performance composites is only possible with Spacer Fabrics 3D characterized by layers of fabric and not connecting yarns. Low weight, good resistance to fatigue and corrosion, combined with the low prices of production and a single-stage manufacturing process, ensure that facilities that use as the preform 3D Spacer Fabrics can replace traditional sandwich structures, widely used in aeronautics and automotive.
These are constituted by two layers resistant spaced and rigidly connected by an element said core, which is typically a material characterized by low resistance and low density, such as foams or honeycomb cells. Their most critical point is the delamination, which causes the separation of the sheets with the consequent loss of mechanical properties. A solution to the critical bonding between skins and core is the replacement of traditional sandwich panels with Spacer Fabrics 3D, in which there is a core of fabrics and the outer surfaces are strongly connected to each other as the yarns of the connecting layer are intertwined with the surface layers. Furthermore, due to the possible presence of solid structures and metallic, the conventional panels can be heavier of the innovative panels obtained from materials reinforced with fabrics provided with cavities and suffer from defects, such as corrosion and propagation of cracks.
The 3D Spacer Fabrics, replacing the traditional metal structures, are used to obtain equal or better performance to the advantage of a weight reduction and CO2 emissions. In 1989, NASA and Boeing have joined forces to create the program, “NASA Advanced Composites Technology” (ACT), to improve the efficiency of composite structures and reduce their manufacturing costs. In fact, the machinery “Advanced Stitching Machine” (ASM) was built to create composite structures for wings with a lighter weight by 25%, while reducing production costs and transaction costs of airlines.
Image Credits: Mecit D., Marmarali A., 2012, Application of spacer fabrics in composite production, Usak University Journal of Material Sciences, 1, pp. 71 – 78; Abounaim Md., Process development for the manufacturing of flat knitted innovative 3D spacer fabrics for high performance composite applications, Dresden, Novembre 2010; www.kth.se; wikipedia.org.
Close-up Engineering – ©Tutti i diritti riservati